- Refractory Raw Materials
Calcined Bauxite Ceramic Foundry Sand Corundum Flint Clay Fluorite Mulite Silica Fume Silicon Carbide Silicon Metal Alpha Alumina Powder Spinel Alumina Bubble Aluminum Powder Bentonite Boron Carbide Ceramic Sand Chromium Oxide Green Cordierite Explosion-proof Fiber Forsterite Fused Silica Graphite High Alumina Cement Kyanite Group Minerals Potassium Feldspar Powdery Instant Sodium Silicate Pure Calcium Aluminate Cement Spherical Asphalt White Clay Zirconite Lignin Synthesis of Ferro Silicon Nitride Homogenized Bauxite
- Refractory Products
- Monolithic Refractories
- Ceramic Fiber Products
- Metallurgical Auxiliary Material
- Industrial Kilns And Parts
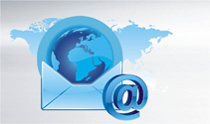
Ceramic Foundry Sand
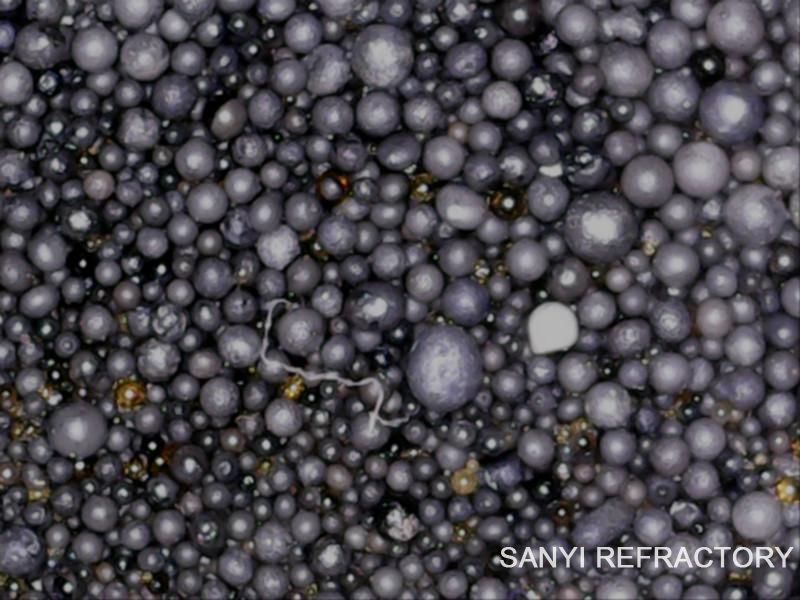
Description
Ceramic foundry sand is made of high quality aluminum-vanadium soil by calcination, electrofusion, granulation, sifting and so on.It has the characteristics of high fire resistance (> 1800 ℃), low angle coefficient (< 1.1, approximate spherical shape), low acid consumption (neutral material), small amount of binder (reducing the amount of binder added by 30%), high strength, no breakage, no poison, etc.It is suitable for sand mold casting (molding sand, core sand), coated sand casting, lost foam casting (filling sand), coating (pearl sand powder) and 3D printing, etc.widely used in automobile engine, automobile parts, large cast steel, cast iron and so on,It is called green environmental protection sand for foundry.
Ceramic foundry sand, also known as fused Ceramsite Sand, is an advanced substitute for quartz sand.The advantages of quartz sand are wide distribution and low cost, but its disadvantages are also obvious: first, large coefficient of expansion, low precision of castings; second, serious sand sticking on the surface of castings, so it is difficult to clear sand. The reason is that at different temperatures, quartz will have a variety of homogenous and heterogeneous crystals, resulting in large volume changes; limited by the degree of refractoriness(the refractoriness of the quartz sand is between 1400 and 1700 DEG C), so the sand and casting parts (holes, grooves and hot nozzles together) are heavily glued and difficult to clean.These shortcomings are especially serious in the production of large steel castings.Ceramic Foundry Sand can overcome these shortcomings, thus greatly improving the quality of castings. It has been proved by practice that Baozhu sand has the following six advantages:
1. Globular granularity: close to the sphere, with a smooth surface and no concave and convex veins. Its fluidity and filling property are good, and good formability and mould strength are obtained.Good collapsibility and easy sand cleaning operation.The amount of binder is less than that of other granular mold sand.
2. Low thermal expansion: The low thermal expansion ratio is the same as that of special sand such as chrome ore sand. Therefore, the size accuracy of castings is high, the number of cracks and surface defects is less, and the yield of castings is high.
3.Good crushing resistance: Ceramic foundry sand has good compactness and high strength, even if it is recycled, it is seldom broken. It can reduce the pollution of the production environment caused by the dust in the foundry production process, be easy to recover, reduce the industrial waste discharge, and be beneficial to the environmental protection.
4.Good fire resistance: The main component is alumina, so the fire resistance is very good. Fire resistance ≥ 1820 ℃ can be used to cast all kinds of metals and alloys.
5.Small accumulation density: Compared with chromium ore sand and zircon sand, the density of ceramic foundry sand is lower. In making the same model, the weight of sand is much lower than that of chrome ore sand and zircon sand, and the production cost is reduced accordingly,it only accounts for 50 percent of the chrome ore sand and only 30 percent of the zircon sand.
6.Neutral materials: Ph 7.6 is stable, resistant to acid and alkali erosion and low acid consumption. Acid and alkaline binders can be used, resin addition can be reduced by 30-50 and sodium silicate ≤ 4.
The fused ceramsite sand for foundry has the characteristics of high strength, good durability, and can be recycled.The use of fused ceramsite sand for foundry can reduce the production of solid waste, reduce the cost of replacing foundry sand, and the product is inert and compatible with most chemical additives.Because of the absence of quartz, the possibility of sand inclusion is reduced. Because of the high fluidity of the fused Ceramsite Sand, the success rate of the thin-walled castings is increased and the number of unqualified castings is reduced to the maximum.It can obtain high filling and compaction cycle with lower energy and reduce casting defects while increasing output.The temperature expansion coefficient of fused ceramsite sand for foundry is very low. Laboratory tests and industrial applications show that the use of fused ceramsite sand can make the casting have more accurate geometric size and precision and reduce the defects caused by expansion.The fused ceramsite sand has the advantages of high temperature resistance,good collapsibility, good grain shape, low crushing rate and strong reuse.The ratio of performance to price far exceeds that of chrome ore sand and zircon sand. It is the ideal moulding material for cast carbon steel and alloy steel castings. The price of fused ceramsite sand is only 1 / 3 of zircon sand and 1 / 2 of chromium iron ore sand, which can greatly reduce the cost of foundry production.
The ceramic foundry sand is optimized by a certain proportion of phenolic resin to improve the tensile strength at room temperature, thus making the surface of the model more smooth, the outline clearer and the initial strength higher. Better performance can be used to realize rapid casting of complex thin-walled parts with fine structure.
The ceramic foundry sand for EPC has the advantages of high fire resistance, good fluidity, strong permeability, low thermal expansion coefficient, good angle shape coefficient and high recovery efficiency. The casting defects of quartz sand or forsterite sand used in traditional casting are completely solved, such as sand inclusion, porosity, scarring, rat tail, etc., which can improve the dimensional precision, improve surface quality, increase finished product rate (up to 99%) and reduce production cost.
The ceramic foundry sand for sandblasting and shot blasting can effectively remove the surface rust, oil and oxide skin of the castings, remove the machining burrs of parts, improve the surface roughness of the parts after heat treatment, and achieve the purpose of purifying the surface.It can also eliminate the internal stress of the part, reduce the surface tensile stress, reduce the deformation degree of the part after heat treatment, improve the wear-resisting and compressive ability of the part surface, and improve the fatigue resistance and corrosion resistance of the material.
The ceramic foundry sand used for ladle drainage sand, the grain shape is close to true circle, the surface is smooth, no concave and convex veins, its fluidity is good,Because of its good fire resistance (fire resistance ≥ 1820 ℃) and no excessive sintering at a certain temperature of molten steel, the thickness of the sintered layer can be reduced.The point contact between the sintered layer particles can effectively reduce the strength of the sintered layer and is beneficial to the pouring of molten steel.Low thermal conductivity, small expansion after heating, can prevent shed materials, to ensure open-pouring self-flow rate.In ladle drainage sand, ceramic foundry sand can be used instead of chrome ore sand, or they can be used proportionally. Its price is much lower than that of chrome ore sand.
Ceramic foundry sand, also known as fused Ceramsite Sand, is an advanced substitute for quartz sand.The advantages of quartz sand are wide distribution and low cost, but its disadvantages are also obvious: first, large coefficient of expansion, low precision of castings; second, serious sand sticking on the surface of castings, so it is difficult to clear sand. The reason is that at different temperatures, quartz will have a variety of homogenous and heterogeneous crystals, resulting in large volume changes; limited by the degree of refractoriness(the refractoriness of the quartz sand is between 1400 and 1700 DEG C), so the sand and casting parts (holes, grooves and hot nozzles together) are heavily glued and difficult to clean.These shortcomings are especially serious in the production of large steel castings.Ceramic Foundry Sand can overcome these shortcomings, thus greatly improving the quality of castings. It has been proved by practice that Baozhu sand has the following six advantages:
1. Globular granularity: close to the sphere, with a smooth surface and no concave and convex veins. Its fluidity and filling property are good, and good formability and mould strength are obtained.Good collapsibility and easy sand cleaning operation.The amount of binder is less than that of other granular mold sand.
2. Low thermal expansion: The low thermal expansion ratio is the same as that of special sand such as chrome ore sand. Therefore, the size accuracy of castings is high, the number of cracks and surface defects is less, and the yield of castings is high.
3.Good crushing resistance: Ceramic foundry sand has good compactness and high strength, even if it is recycled, it is seldom broken. It can reduce the pollution of the production environment caused by the dust in the foundry production process, be easy to recover, reduce the industrial waste discharge, and be beneficial to the environmental protection.
4.Good fire resistance: The main component is alumina, so the fire resistance is very good. Fire resistance ≥ 1820 ℃ can be used to cast all kinds of metals and alloys.
5.Small accumulation density: Compared with chromium ore sand and zircon sand, the density of ceramic foundry sand is lower. In making the same model, the weight of sand is much lower than that of chrome ore sand and zircon sand, and the production cost is reduced accordingly,it only accounts for 50 percent of the chrome ore sand and only 30 percent of the zircon sand.
6.Neutral materials: Ph 7.6 is stable, resistant to acid and alkali erosion and low acid consumption. Acid and alkaline binders can be used, resin addition can be reduced by 30-50 and sodium silicate ≤ 4.
The fused ceramsite sand for foundry has the characteristics of high strength, good durability, and can be recycled.The use of fused ceramsite sand for foundry can reduce the production of solid waste, reduce the cost of replacing foundry sand, and the product is inert and compatible with most chemical additives.Because of the absence of quartz, the possibility of sand inclusion is reduced. Because of the high fluidity of the fused Ceramsite Sand, the success rate of the thin-walled castings is increased and the number of unqualified castings is reduced to the maximum.It can obtain high filling and compaction cycle with lower energy and reduce casting defects while increasing output.The temperature expansion coefficient of fused ceramsite sand for foundry is very low. Laboratory tests and industrial applications show that the use of fused ceramsite sand can make the casting have more accurate geometric size and precision and reduce the defects caused by expansion.The fused ceramsite sand has the advantages of high temperature resistance,good collapsibility, good grain shape, low crushing rate and strong reuse.The ratio of performance to price far exceeds that of chrome ore sand and zircon sand. It is the ideal moulding material for cast carbon steel and alloy steel castings. The price of fused ceramsite sand is only 1 / 3 of zircon sand and 1 / 2 of chromium iron ore sand, which can greatly reduce the cost of foundry production.
The ceramic foundry sand is optimized by a certain proportion of phenolic resin to improve the tensile strength at room temperature, thus making the surface of the model more smooth, the outline clearer and the initial strength higher. Better performance can be used to realize rapid casting of complex thin-walled parts with fine structure.
The ceramic foundry sand for EPC has the advantages of high fire resistance, good fluidity, strong permeability, low thermal expansion coefficient, good angle shape coefficient and high recovery efficiency. The casting defects of quartz sand or forsterite sand used in traditional casting are completely solved, such as sand inclusion, porosity, scarring, rat tail, etc., which can improve the dimensional precision, improve surface quality, increase finished product rate (up to 99%) and reduce production cost.
The ceramic foundry sand for sandblasting and shot blasting can effectively remove the surface rust, oil and oxide skin of the castings, remove the machining burrs of parts, improve the surface roughness of the parts after heat treatment, and achieve the purpose of purifying the surface.It can also eliminate the internal stress of the part, reduce the surface tensile stress, reduce the deformation degree of the part after heat treatment, improve the wear-resisting and compressive ability of the part surface, and improve the fatigue resistance and corrosion resistance of the material.
The ceramic foundry sand used for ladle drainage sand, the grain shape is close to true circle, the surface is smooth, no concave and convex veins, its fluidity is good,Because of its good fire resistance (fire resistance ≥ 1820 ℃) and no excessive sintering at a certain temperature of molten steel, the thickness of the sintered layer can be reduced.The point contact between the sintered layer particles can effectively reduce the strength of the sintered layer and is beneficial to the pouring of molten steel.Low thermal conductivity, small expansion after heating, can prevent shed materials, to ensure open-pouring self-flow rate.In ladle drainage sand, ceramic foundry sand can be used instead of chrome ore sand, or they can be used proportionally. Its price is much lower than that of chrome ore sand.
Ceramic Foundry Sand | ||
Item | CFS-75 | |
Chemical Content,% | Al2O3,% | 70-80 |
Fe2O3,≤% | 5 | |
TiO2,≤% | 2.5 | |
SiO2 ,% | 10-12 | |
Physical Properties | True Density ≥g/cm3 | 2.9 |
Tap Density,g/cm3 | 1.95-2.05 | |
Thermal Expansion,1000℃,10Min,% | 0.13 | |
Thermal Conductivity,W/M.K,1200℃ | 5.27 | |
Refractoriness, ≥ | 1790 | |
Particle Shape | Spherical | |
Angular Coefficient,≤ | 1.1 |
SIZE AVAILABLE:
10-14Mesh
20-30Mesh
40-70Mesh
100-140Mesh
170Mesh
200Mesh
In addition to the above dimensions, we can also process according to your requirements.
Leave a message: Please fill in your information and we will contact you soon.